
Textile Underwear Fabric Printing and Dyeing Process
- By:Teresa Zhang
- Date:2023/11/22
Textile printing, dyeing and finishing is a huge systematic project, involving multiple processes such as raw materials, semi-finished products, weaving, printing and dyeing, and finishing. Among them, spinning, weaving, printing, dyeing and finishing are three relatively independent industries.
In the printing and dyeing industry, according to different raw materials, different yarn types, different fabric structures, and different printing and dyeing requirements, the process flow is not a completely fixed model, such as chemical fiber textile printing and dyeing, wool textile printing and dyeing, and silk reeling in the silk industry. The differences between weaving, dyeing and finishing are quite large, and there is basically no way to learn from each other.
So, let us first understand the conventional processes in the three industries of spinning, weaving, printing, dyeing and finishing, so as to a simple understanding of the spinning, printing and dyeing industry, and at the same time have an overall impression of the source of underwear fabrics.
The main processes of spinning process: cleaning, carding, combing, drawing, roving and spun yarn.
The main processes of the weaving process: winding, warping, sizing, drawing in, weaving and finishing.
These are the main processes, and each company will have slightly different processes based on their products and their own needs. Let's take cotton as an example to share with you the conventional cotton textile printing and dyeing process.
Cotton textile printing and dyeing process: blank preparation - seam head - singeing - cold rolling car - deboiling and bleaching - mercerization - pre-determined tenter - stocking - printing (flat screen or rotary screen printing) --Steaming machine--Soaping machine--Finishing and shaping--Pre-shrinking machine--Calender--Quality inspection and packaging.
1. Singeing
Usually, after the gray fabric enters the printing and dyeing factory, it first needs to go through processes such as inspection, turning, batching, matching (matching: the front and back of two pieces of gray fabric, the same side is put together) and seaming, and then undergoes singeing processing. Singeing: The singeing process looks very magical. At the scene, you will see the fabric quickly passing through the high-temperature flames, while the cloth slides quickly on the fierce flames without burning. It's really a bit of a state of "not even a leaf touches me among a hundred flowers".
This is because the cloth body is relatively tight and heats up slowly. Before it reaches the ignition point, it has left the flame or red-hot metal surface, thereby achieving the purpose of burning off the fluff without damaging the fabric. Reason: The unsinged cloth surface has too much fluff, varying lengths, poor smoothness, and easy staining. It is easy to lose hair during subsequent dyeing and finishing processes, resulting in printing and dyeing defects.
Significance:
a. The purpose of singeing is to burn off the fluff on the cloth surface to make the cloth surface smooth and beautiful, and to prevent uneven dyeing and printing defects caused by the presence of fluff during dyeing and printing. Improve the gloss of the cloth surface and improve the smoothness;
b. Improve anti-pilling properties (especially chemical fiber fabrics);
c. Improve style, singeing will make the fabric stiff.
Cold rolling car: a process after singeing, the gray cloth needs to be cooled for more than 20 hours.
2. Desizing, scouring and bleaching
Desizing: The sizing on the gray cloth should be removed before scouring. This process is called desizing. In order to increase the wear resistance, smoothness and antistatic properties of warp yarns in weaving, increase their strength and improve their weavability, sizing is required before weaving. The sizing on the gray fabric affects the water absorption performance of the fabric, and also affects the quality of the dyeing and finishing products, and increases the consumption of dyeing chemicals. Therefore, the sizing should be removed before scouring. This process is called desizing. That is to remove it from the fabric.
Scouring: Its purpose is to remove fiber impurities (natural impurities, artificial impurities) and improve fabric processing properties, especially wetting properties. When cotton fibers grow, they are accompanied by natural impurities (pectin, waxy substances, nitrogen-containing substances, etc.). After desizing the cotton fabric, most of the sizing and some natural impurities have been removed, but a small amount of sizing and most of the natural impurities still remain on the fabric. The presence of these impurities makes the cotton fabric surface yellower and has poor permeability. At the same time, due to the presence of cotton seed hulls, the appearance quality of cotton cloth is greatly affected. Therefore, the fabric needs to be scoured in high-temperature, concentrated alkali solution for a long time to remove residual impurities.
Bleaching: After scouring cotton fabrics, due to the presence of natural pigments on the fibers, their appearance is not white enough. When used for dyeing or printing, the brightness of the color will be affected.
Purpose of bleaching: removing pigments and improving whiteness are the main purposes of bleaching processing.
3. Mercerizing
Mercerization: Using a concentrated alkali solution to treat cotton woven fabrics, the surface will show a silky luster, and more importantly, its dimensional stability will be improved, that is, the cotton woven fabrics will be shaped. This processing process is called Mercerization or Mercerizing. The significance of mercerizing treatment: a. Improved dimensional stability and reduced shrinkage; b. Changes in mechanical properties such as reduced breaking strength; c. Improved adsorption; d. Silky luster appearance.
4. Stenter
Tenting is to elasticize the warp and weft of the fabric again to make the fabric have the same width and density in the warp and weft directions, thereby increasing the dimensional stability of the fabric.
5. Mixing and shaping
Jacquard varieties undergo varying degrees of sizing before calendering, allowing the sizing to adhere to the fiber surface to prevent the fabric from shrinking. Sizing has a softening effect and promotes friction between fibers.
6. Printing
There are currently two most widely used printing methods, rotary screen and flat screen printing. Due to the small tension, it is not easy to deform, the colors are bright and full, and the screen printing defects are less, so it is especially suitable for multi-variety production. Rotary screen and flat screen printing both require screens in terms of installation. It originates from pattern printing, which is a printing method that uses paper plates, metal plates or chemical engraving to create hollow patterns.
The rotary screen uses a nickel circular metal mesh, while the flat screen uses a screen mesh stretched on a metal or wooden rectangular frame. Flat screen printing is divided into manual (table printing) and mechanical (flat screen printing). Due to different printing methods, the size has a certain allowable range, and the flat screen size is 305~1200mm. Generally, the circumference of rotary screen printing mesh is 640mm, 820mm, and 1018mm. The perimeter is a multiple of the loop of the pattern.
The characteristic of the rotary screen is that the patterns are connected and there is no printing. The screen of flat screen printing is square, so its circulation is not restricted, and the flat screen has connecting spaces.
Generally speaking, rotary screen printing has the largest output, generally 3,500 yards per hour. The speed depends on the difficulty of the pattern. Flat screen printing fineness and flower return size are better than rotary screen, but the production efficiency is not as fast as rotary screen. In actual selection, you need to weigh whether to choose a rotary mesh or a flat mesh based on the fabric use, pattern size, fabric, etc.
7. Steaming and soaping
Steaming: After textile printing, except for ice dyes and soluble vat dyes, general dyes must be steamed.
Purpose: to enable the printed textiles to complete the moisture absorption and temperature rise of the fiber and color paste film, accelerate the reduction of the dye and the dissolution of the dye on the fiber, so that the dye can diffuse into the fiber and be fixed on the fiber, and then diffuse into the fiber to produce color fixation. The steaming process conditions vary with the nature of the dye and fiber.
Soaping: It is a very necessary and important process after steaming. During the soaping process, the soaping agent interacts with the dye through physical and chemical interactions, and utilizes the dispersion, suspension, and complexing effects of the soaping agent to prevent it from sticking to the fabric, thereby improving soaping fastness and preventing staining.
8. Pre-shrunk finishing
During the printing and dyeing process, the fabric is stretched by mechanical tension and has internal stress. When the fabric is wetted, the internal stress relaxes and causes a shrinkage effect. Therefore, in actual production, the fabric must be mechanically preshrunk to reduce the shrinkage of the cotton fabric. The shrinkage rate stabilizes the size of the finished product, keeps the fabric width neat, and increases the added value of the product.
9. Calendering treatment
Calendering treatment also called calendaring, a process of fabric finishing, a finishing process that utilizes the physical plasticity of fibers under high-pressure or high-temperature conditions to flatten or create patterns on the surface of the fabric to increase the luster of the fabric. Similar to ironing, surface flattening and ironing methods are used to give the fabric a special luster, increase the brightness of the fabric, and make the fabric drape well and smooth.
10. Quality inspection and packaging
At this point, the printing and dyeing of the cloth is complete. Quality inspection and roll packaging, if there is any leakage in the pattern, the printing will need to be trimmed manually and packaged for shipment.
- Xiamen Unitex Trade CO.,LTD.
- Website: www.unitexunderwear.com
- E-mail: [email protected]
- Tel: 0086-186 5081 3853
-
Skype
will_linxb (Will Lin)
-
WhatsApp
CONTACT US

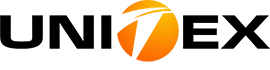
Xiamen Unitex Trade Co., Ltd.
We are always providing our customers with reliable products and considerate services.
If you would like to keep touch with us directly, please go to contact us